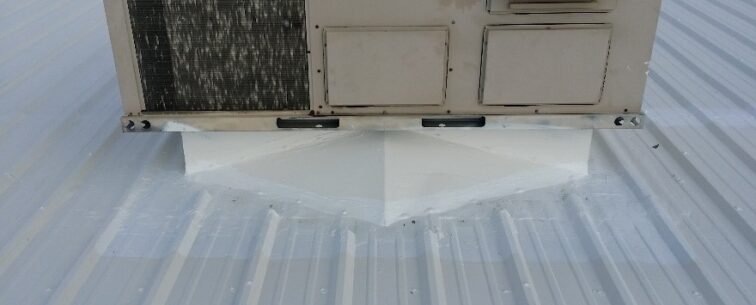
Company Serviced/Roof Repair: Avera Commerce Center
Details:
Avera Commerce Center is a property located in Stafford, Texas managed by Transwestern Property Management. The property consists of a total of sixteen concrete tilt wall buildings with galvanized R panel metal roofs. The buildings spanned three streets and had a total of 278,000 square feet of roof. The roofs were in very poor condition with a tremendous number of patches that had failed and were trapping moisture causing rust. The HVAC curbs did not have crickets so during and after a rain, the water would pond on the uphill side of the curb. This caused severe rust and failure of many of the roofs. Many of the EPDM washers on the sheet metal screws securing the roof panels were dry rotted and had the potential to leak. Some of the screws had become loose and partially unscrewed. Every single one of the 16 building had leaks of varying degrees. Structure Roof and Wall Solutions was brought in to see if they could offer a solution to the owner at a lower cost than a re-roof. Transwestern had done research and come up with three different options. The first option was to replace all of the metal roofs which would have cost roughly $2,500,000. Option two was to install deck board over the metal with a single ply roofing system which would have cost roughly $1,600,000. The third option was Structure Roof and Wall Solution’s fluid applied reinforced roofing system at just over $800,000.
Specs:
Structure Roof and Wall Solutions (SRWS) was hired for the project and started in January of 2017. The first step was properly cleaning and prepping the entire existing roof. SRWS cleaned the roofs utilizing their soft chemical restoration system and low-pressure rinse. They then removed all existing patch material to ensure no rust was present. After this, they tightened all the screws and replaced rusted or broken screws. Custom built galvanized metal roofing crickets were installed to divert the water around the one hundred twenty-six HVAC curbs. All roof penetrations, horizontal seams and
vertical seams where the gable flashing attached to the roof received a three-course of elastic mastic, polyester fabric, and primer coat. Once all of the prep work was completed, the task of actually applying the fluid applied reinforced roofing system could commence. The fluid applied system consisted of two coats of acrylic base coat and one coat of acrylic top coat.
Results:
The roofs were in worse shape than originally anticipated and took quite a bit of time to properly prepare them for the coating application. Transwestern was very happy with the finished product and Structure Roof and Wall Solutions. Upon completion of the job, the building owner received a transferable, renewable, 10 year no leak warranty. In addition to the upfront savings being substantial, because the IRS classified this project as a maintenance expense, the owner also was able to use the entire cost of the job as an expense in one calendar year. The buildings now have a monolithic fluid applied system that has stopped the leak issues. The custom built crickets have been successfully diverting the water to stop ponding and rusting in those areas.